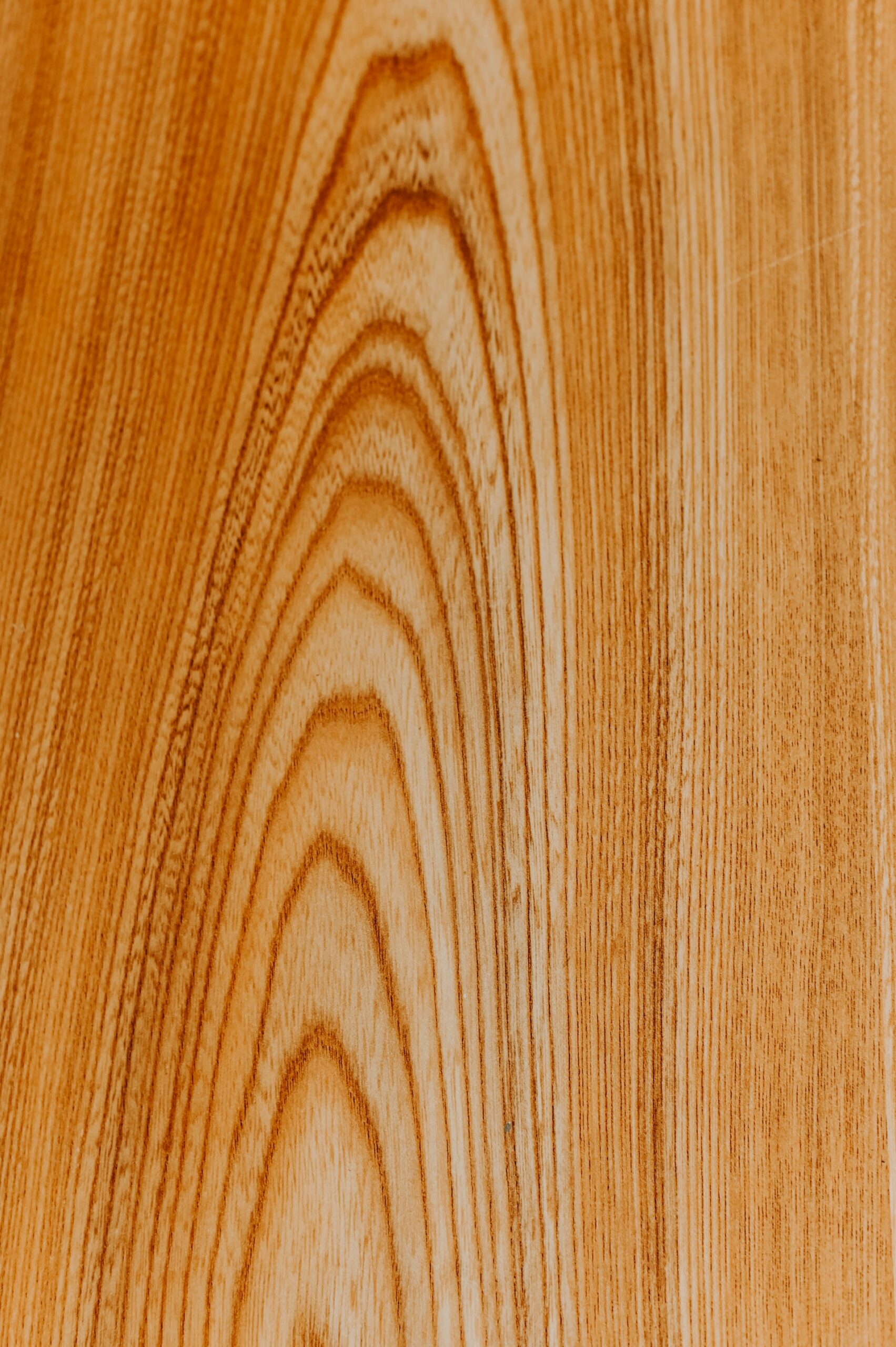
The Advantages of Using Lacquer
In wood-finishing lacquer is a modern technique that is particularly popular for use on high-end furniture. Since the mid-1900s the development and use of lacquer as a finishing agent has almost reduced the use of shellac to insignificance.
Lacquers are similar to finishes like varnish and urethanes but are applied differently. Generally, lacquers are sprinkled onto the surface instead of being brushed on or hand-rubbed with a cloth. Like varnish or urethane but unlike oil, lacquer finishes form a film on the wood surface instead of saturating the wood grain.
Some of its best features include its water-resistant, fast-drying capabilities and its ability to maintain liquidity as it ages. It is in such high demand for furniture finishing’s because lacquer does not tend to yellow with the passage of time, provides a secure seal against liquids, and needs little or no maintenance.
Lacquer is made with plant resins that are mixed with a drying solvent. Lacquer features the fastest drying times compared to most other common protective finishes. This provides several advantages such as a distinct improvement in turnaround time. Lacquer-finished surfaces often take less than half the time to dry as those finished with other products; provide improved surface quality due to their ability to reduce dust adhesion; reduce in occupied floor space during drying time which enhances the abovementioned improvements in production cycles.
Advantages of Lacquer
- Lacquer is a long-lasting, tough finish that outlasts most other competitive products without chipping or flaking.
- The finish remains clear for many years without yellowing which is often associated with products like varnish, shellac, or polyurethane.
- It is versatile and comes in three varieties – dull; medium; high-gloss
- The formula is much thinner than other finishing products allowing it to penetrate deeper, providing a durable protective seal from the inside out.
- No more than two coats of lacquer are needed to get a good-looking, high gloss sheen. This avoids product build-up and saves on production costs.
- It is considerably less expensive to purchase than other products and needs less labour as it needs only two coats two to obtain a quality finish.
One of the more attractive features, from a carpenter’s perspective, is the colour and tone stability of a lacquer finish throughout the drying cycle. Whereas many other products are prone to change in shade and tone while applying the finish, making it difficult to gauge the end result, lacquer finishes,(whether clear or tinted), retain the same colour and tone throughout the drying and curing stages. This gives a good indication of what the end result will look like from the very first application. The cured lacquer surface can be matte, satin, or polished to a mirror-like high gloss finish depending on the result desired. Subject to normal use, once polished, the lacquer finish will maintain its lustre throughout the life cycle of the finished piece.
Disadvantages of Lacquer
If proper precautions are not taken during its application some disadvantages may occur with the use of lacquer:
- Blushing may occur when moisture is present inside the airline due to high humidity or a room that is too cool during application. Blushing is detected as milky-white blotches on the surface of the wood after the lacquer layers have dried. This moisture in the finish will remain trapped until corrected.
To prevent blushing always check the airlines for any moisture that may be present and ensure that the room you are working in is adequately ventilated and free of moisture. - Fish-Eye is another blemish caused by contaminants in the lacquer, on the wood surface, or in the airline. Appropriately named, these defects resemble the eye of a fish with a round crater and can be numerous. Contaminants such as oil, silicone, wood cleaners, or other particles that get into the lacquer can cause fish-eye. Always use clean equipment and lacquer to avoid fish-eye from forming and spoiling the end result of the finish.
- Orange peel is usually caused when the temperature in the room is too cool. True to its name this type of defect looks like orange skin. The rough and ugly appearance may not be apparent until after the lacquer has dried. It can be caused when the lacquer is allowed to dry too fast, trapping air underneath the surface which forms bubbles. It can also be caused by moving the applicator gun too fast. Try thinning the lacquer with a thinner to reduce the likelihood of bubbles forming.
If you experience any of the above problems while using lacquer, stop working on your project and run some test sprays on scrap wood before continuing. Once you have detected the problem, apply the necessary steps to remedy it, then re-test to ensure that the lacquer goes on flat without any of the abovementioned problems. If you take care to ensure that all the lacquer and surface area is clean and the environment is neither too hot nor cold, you shouldn’t have any problems with the finished product.